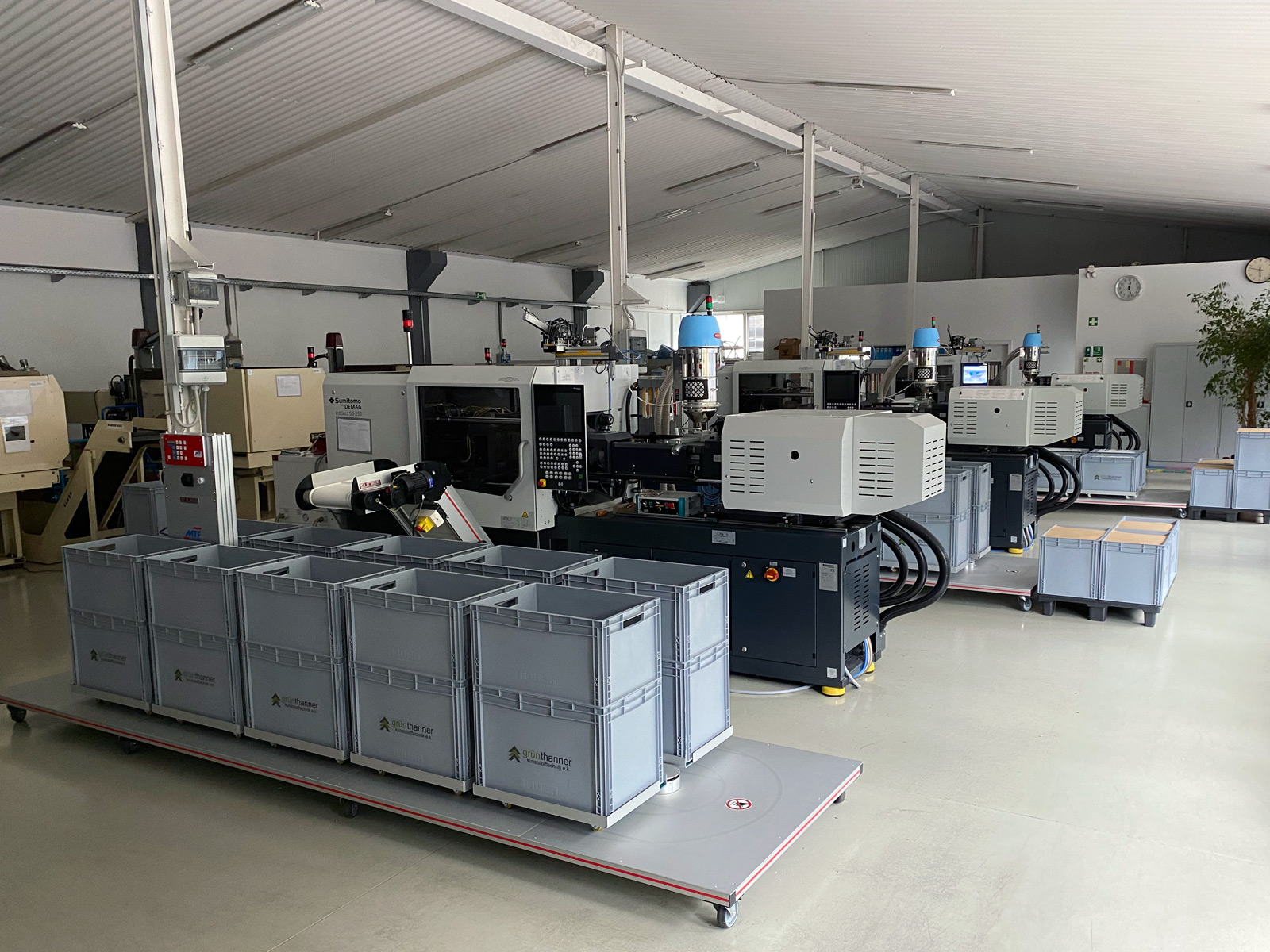
About us - Grünthanner-Kunststofftechnik
From mold construction to plastics technology
History
Formation in 1979
The small enterprise Formenbau Hans Grünthanner of Nuremberg became Grünthanner Kunststofftechnik – Formenbau when his son-in-law Hans Romeis joined the company in 1979.
This was the start for manufacturing own plastic parts using injection molding technique apart from manufacturing forms for customers. At that time, the machines were still manually operated, and production was very time-consuming. Further development then made it possible to buy automatic machines, something that brought about substantial relief for the staff and under the aspect of time.
Goods were made by order for various customers from the most different fields: painters’ needs, toys, medical equipment, various technical articles. Own products like our hangers for infusion bottles came along and were sold all over Europe.
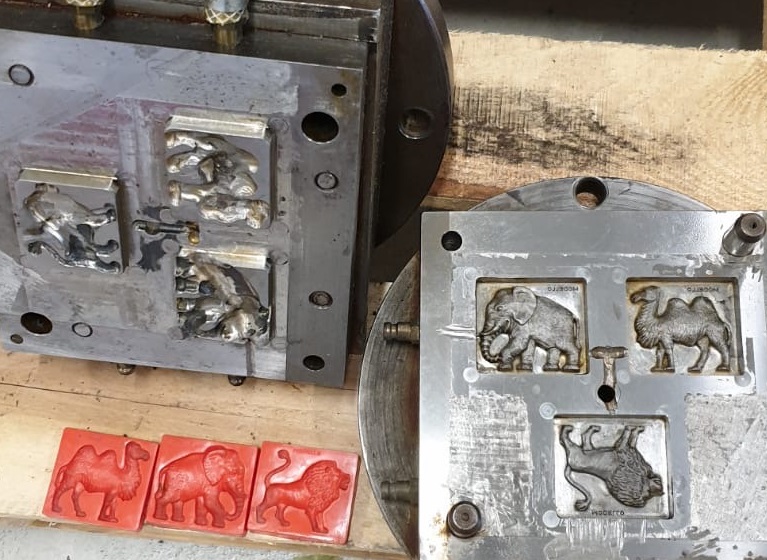
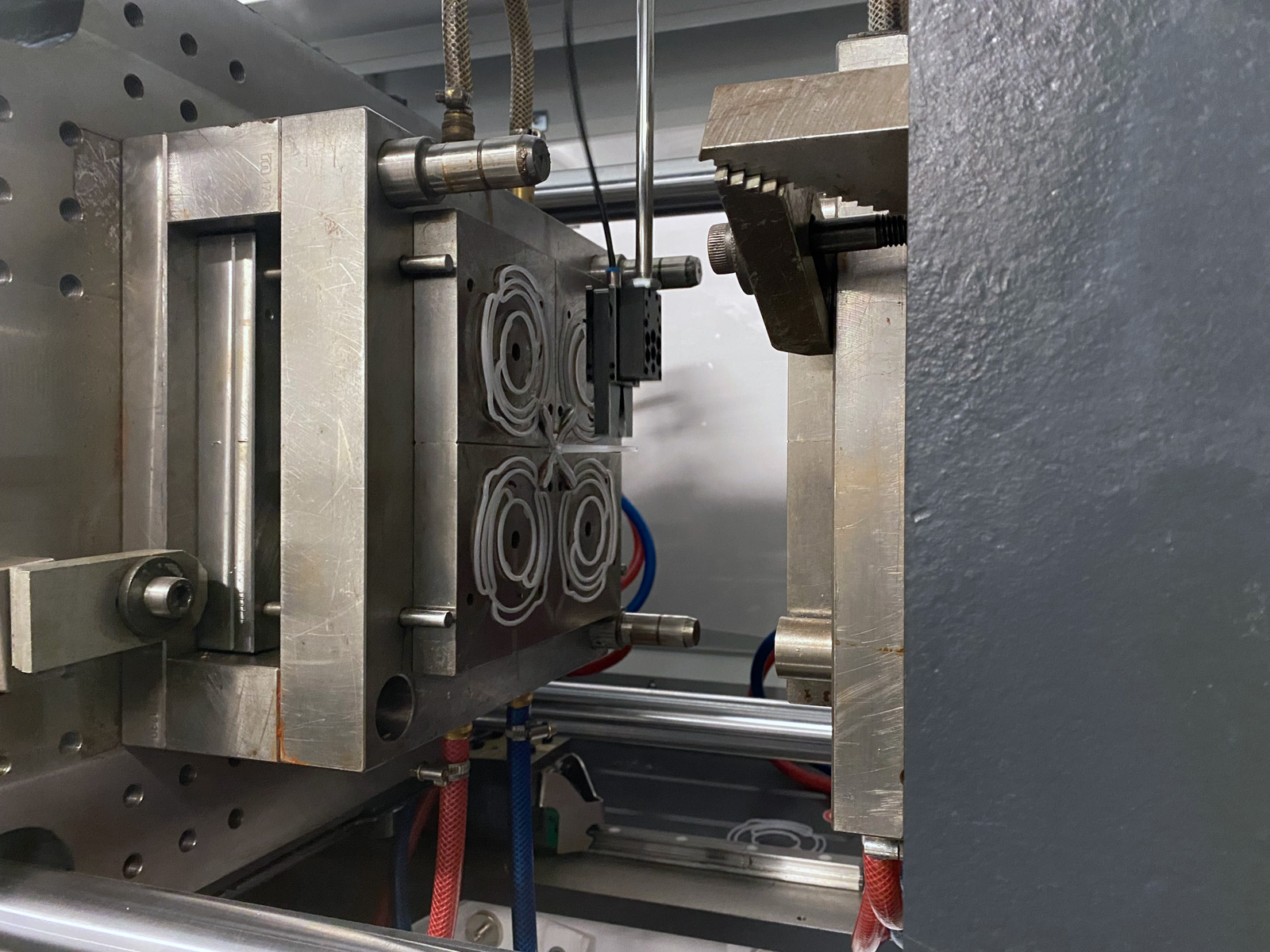
Expansion in 2001
In 2001, Grünthanner Kunststofftechnik – Formenbau moved from Nuremberg to Burgthann in a factory building of its own. The new location offered more space and better transport connections. More machinery was bought, and the group of customers enlarged.
Company takeover in 2019
Some fresh air was breathed into the company when Hans Romeis took it over in 2019. Hans Grünthanner retired due to old age and the managing director of many years finally took over the company himself. The firm changed to Grünthanner-Kunststofftechnik e.K. and Hans Romeis’ daughter Stephanie Dietzsch joined the company.
The factory was continuously modernized and equipped with new electrical machines. By applying new technical aids, production processes were made more easy for the staff.
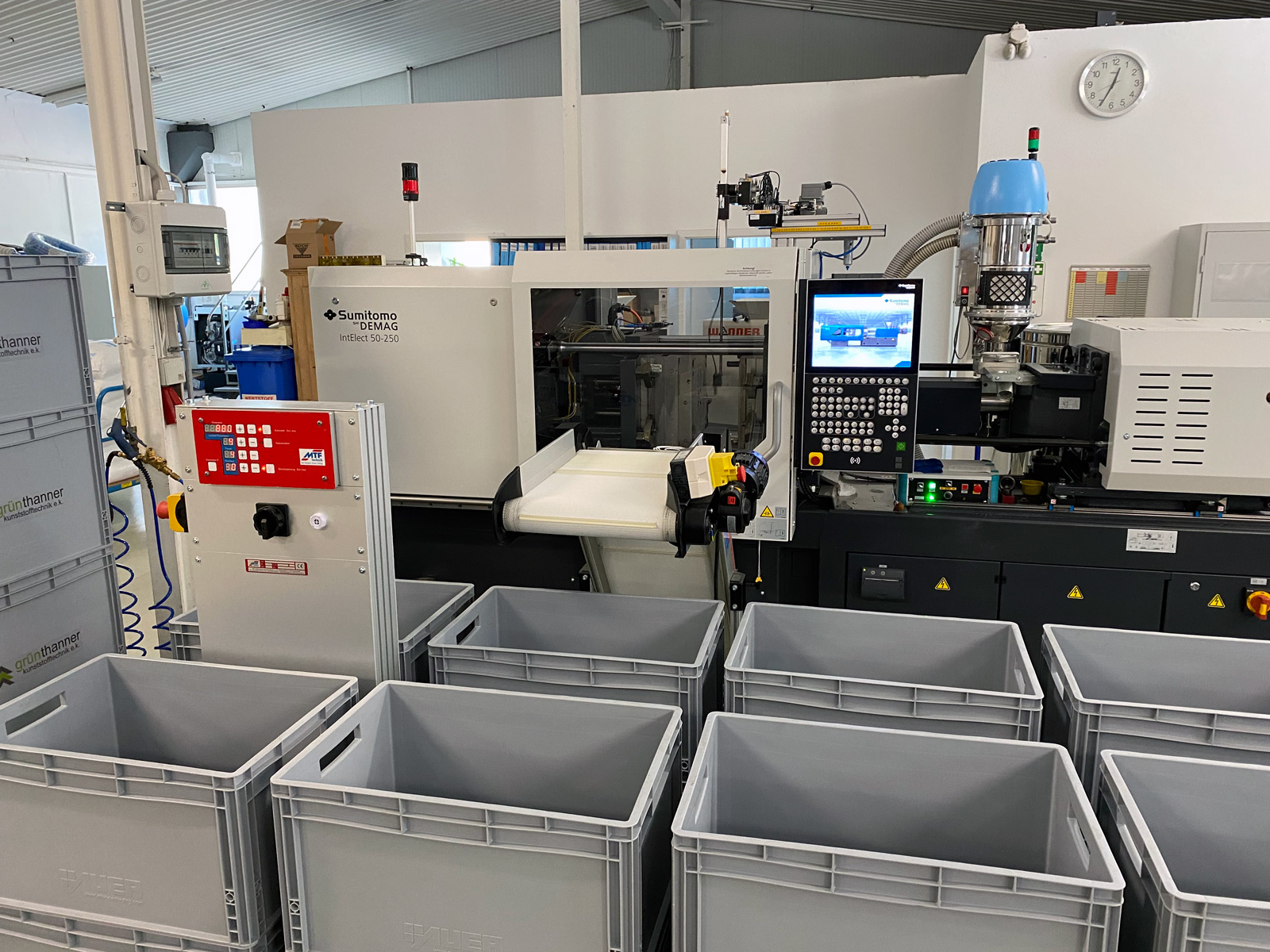
Partnerships
A continuous cooperation in partnership with customers and suppliers is important for us. For this objective, we primarily rely on regional partners for mold construction. As respects packaging, we closely work together with workshops for handicapped people, amongst others.
Sustainability
To work in a sustainable way is very important for us. By investing in new and more efficient machinery we save power and resources. Whenever possible, we re-use our re-granulate to spare resources and avoid waste. We permanently strive for making our production more environmentally friendly, for example by installing LED lighting, using new packaging materials and energy-efficient devices. Some of the company cars have already been replaced by electric cars.
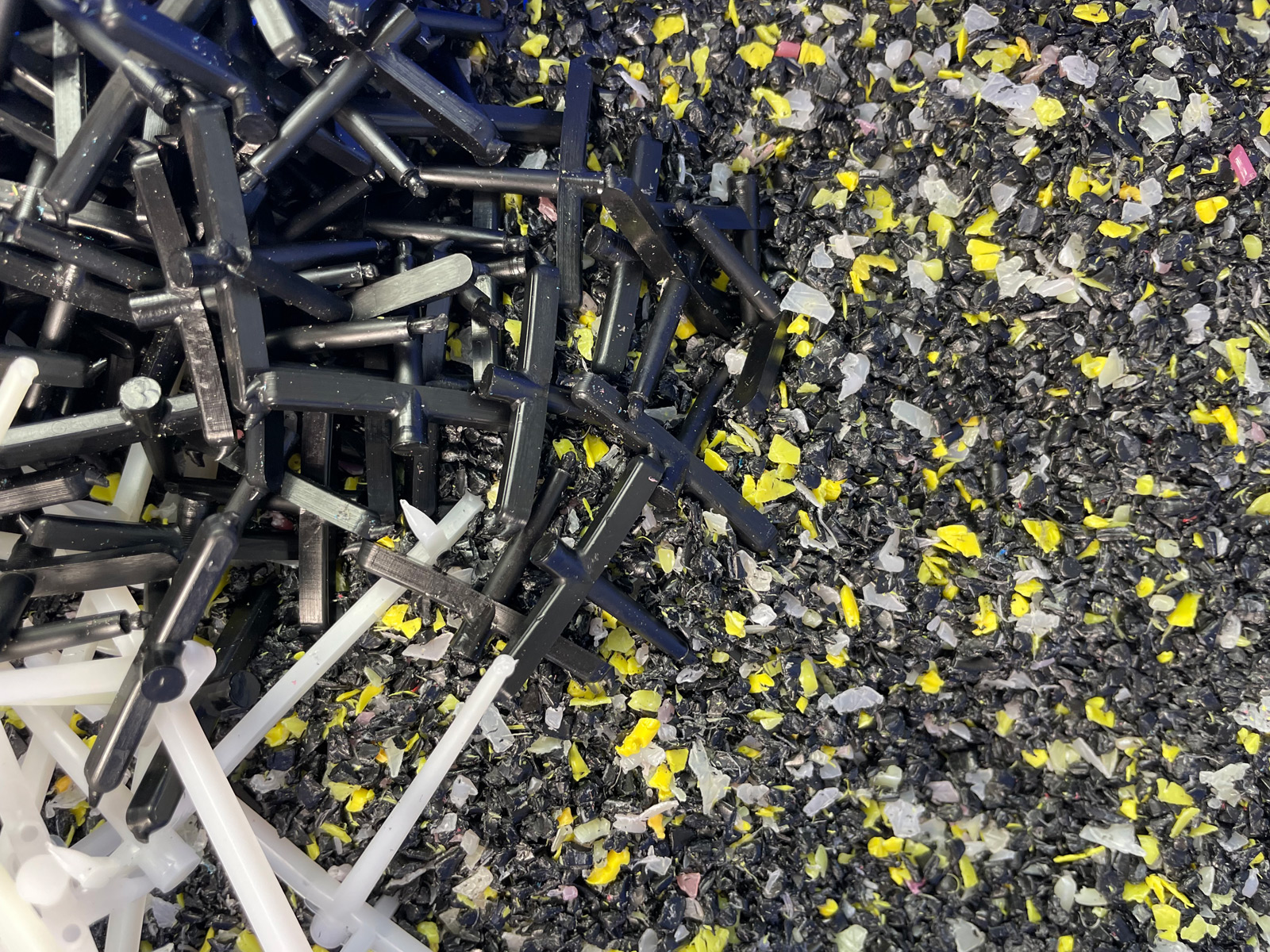